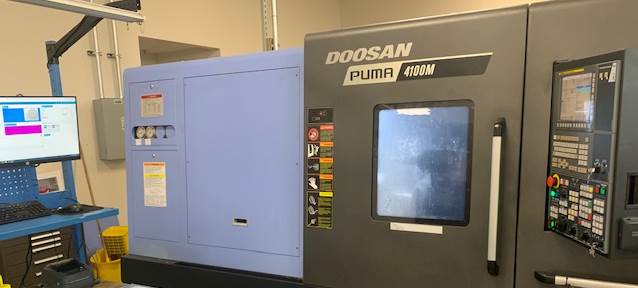
OSM Streamlines Its Internal Operations and Reduces Quote Time by 50% Through Paperless Parts and Plex Systems Integration
The Challenge
One Source Manufacturing (OSM)’s former ERP system lacked key aspects of the shop’s internal operations and did not meet the shop’s quoting needs. This hindered OSM’s efficiency and ability to grow its team and customer base.
The Solution
Paperless Parts and Plex Systems integrate to deliver a cloud-based, highly flexible, customized quoting experience to OSM that allows the shop to quote faster, further empower its team, and streamline its internal operations.
The Results
-
The Paperless Parts and Plex Systems integration reduces quote time by over 50%, enabling OSM to generate more quotes
-
The integration streamlines internal operations, enabling more innovation and growth within OSM’s team
-
OSM harnesses the comprehensive data the integration provides to boost efficiency, improve organization, and stay ahead of the competition
Background
For nearly twenty-five years, One Source Manufacturing Technology (OSM) has been a leading provider of precision machine work, serving a broad range of customers such as those in the aerospace, energy, and semiconductor industries. In addition to precision machining—CNC Milling, CNC Lathe—the Texas-based machine shop offers diverse capabilities to its customers, including wire EDM, finishing, laser marking, and precision lapping. In recent years, OSM has seen tremendous shop growth, from expanding its customer base into new industries to bringing more people onto the OSM team.
Challenge
OSM’s previous ERP system was limited to purchasing and production, leaving its quoting process and many of its internal operations difficult to manage. OSM was able to curtail the inefficiencies associated with its former ERP system, but it became increasingly more difficult and ultimately required additional resources. The inability to use existing accounting in the prior ERP system created inadvertent redundancies making it more challenging to accurately manage critical WIP and other cost related issues. The existing quoting module lacked details and flexibility that aligned with expanding customer demands. Eventually, OSM resorted to a multitude of work arounds to ensure customer needs were met. This approach offered little value in the long run.
Tim Schneider, OSM’s Vice President of Operations, recognized that the shop was poised for significant expansion that the former ERP system and quoting process would not be able to accommodate. “The old ERP system wasn’t helping us with our quoting with the many gaps and lack of effective analysis,” Tim said. “That made it hard to be efficient and focus on growing our customer base.”
The system lacked effective communication tools that ultimately required additional work arounds. Email communication became the primary tool to address gaps within the system. Reliance on email chains further increased the risk of internal and external communication errors. This concern became more prevalent with increased business growth.
Tim and his team knew they needed a solution that would achieve its expectations of an ERP system while also resolving its quoting challenges. For over a year, Tim researched more than a half dozen ERP systems, each of which fell short of its organizational needs, neglected the quoting process, and lacked the sort of flexibility and customization that OSM needed to thrive.
Solution
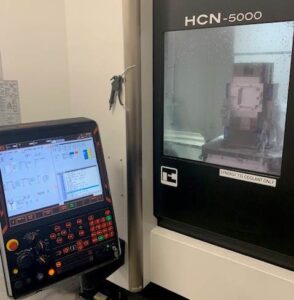
After a long search for an ERP system, Tim discovered the Plex Smart Manufacturing Platform, which automates business processes and tracks data from the plant floor to the top floor for unmatched visibility, quality, and control. The Plex platform covered much of what OSM needed in a solution: accounting, quality control, purchasing, and production, all through an intuitive, purpose-built interface that the entire team would benefit from. While Plex alleviated many of the organizational burdens OSM had been struggling with, Tim still needed software that could pair with Plex to streamline the shop’s quoting process.
When Tim came across Paperless Parts, it was clear that the software’s flexibility, internal collaboration capabilities, and centralization went above and beyond what OSM was looking for in a quoting solution. “We knew that Paperless Parts would allow us to redefine the way we were quoting to make it work for our shop,” Tim said.
“At a time when manufacturers are looking at ways to use technology to operate more efficiently and grow, we see tremendous value in the combined power of Plex and Paperless Parts. Together, we are unleashing new and better ways for our mutual customers to estimate complex jobs and win more without disrupting their existing tech stack or overarching workflows.” – Brad Hafer, Plex GVP, Corporate Development, Plex Systems
The smooth, simultaneous implementation of both Plex and Paperless Parts gave the team at OSM the confidence that both solutions would give them the support they needed when it came to integration. With Plex, OSM went about the ERP transition through a Plex Partner who helped the shop map out and customize its processes, as well as plan a phased approach to using the software. With Paperless Parts, OSM also had a seamless onboarding experience:
“Kudos to the Paperless Parts team, as it was a very quick and highly-supported process,” Tim said. “We’re still closely supported by the team today, which is a big deal for us because that support is huge.”
The integration of Paperless Parts and Plex together was key for OSM’s improved efficiency in every corner of its shop. Not only does OSM now have the benefits of both Paperless Parts and Plex, but their integration ensures that OSM has one centralized framework for its ERP and quoting needs as it had initially set out to find. This centralized quoting process has eliminated the need for double data entry into more than one system, enabling OSM to reduce quoting time by over 50% which equates to their ability to generate more quotes. “With the integration, we can now convert and facilitate orders right out of Paperless Parts and have a starting point for that information in Plex, which gives us a basis for what we can refine in engineering,” Tim said.
In addition to organization, the integration has shaped how Tim and his team work with internal data. As a result, they are seeing massive improvements in how they are processing parts out on the shop floor, as well as with their on-time delivery and costs. The team is even able to precisely break down the shop’s win rates to assess processes with higher and lower loss rates.
Through the integration, the OSM team has also seen a drastic shift in how its team operates on a day-to-day basis. Paperless Parts and Plex together empower the team to focus on different aspects of growing the shop, as well as pinpoint areas for improvement based on the data that is now at its disposal. “Before [Paperless Parts], we just felt stuck in so many ways. The innovation around here today has improved dramatically due to the level of visibility we now have into the quoting process. The folks on our team can now make adjustments as they see fit,” Tim said.
Results
Through the Paperless Parts and Plex integration, OSM:
- Transitioned to a simpler and more intentional form of internal communication: Before using Paperless Parts and Plex, OSM relied heavily on email communication for all organizational and quoting aspects of the business. This created a lot of unnecessary noise that increased risk of miscommunication that could lead to decreased shop productivity. With the Paperless Parts and Plex integration, OSM is now able to harness Paperless Parts’ strong internal collaboration and Plex’s processes to establish better lines of communication across its team.
- Gained a better understanding of its data: For Tim, the biggest difference between OSM before and after implementing Paperless Parts and Plex is that the shop now has a single source for all of its data. This helps OSM make better decisions regarding its quoting and operations every day.
- Established a comprehensive system for its organizational and quoting needs: Tim recognized that though there was not a single solution for managing all of the shop’s organizational and quoting needs, he could achieve a single system through the integration of Paperless Parts and Plex. This integration eliminated the need for double data entry and reduced quote time by 50%. Paperless Parts extends the capabilities of the Plex platform for greater speed and flexibility in the estimating and quoting process.
- Accommodated its aspirations for growth: OSM’s former ERP system and quoting process were not suitable for the projected growth of the shop, both internally and from a customer perspective. The integration between Paperless Parts and Plex provided OSM with the infrastructure to grow by offering the flexibility to quote the way they need to according to their business processes.
- Empowered its team: Paperless Parts has given the OSM team visibility into the entire estimating and quoting process, enabling them to constantly seek potential improvements in the shop’s processes, bringing about the creativity and innovation that is highly valued at OSM.
As the OSM team looks towards the future of the Paperless Parts and Plex integration, Tim is excited to see how both cloud-based solutions together continue to improve the shop’s operations. Moreover, Tim is confident that the integration will continue to give OSM a competitive edge in contract manufacturing. “The name of the game is staying competitive and providing customer value,” Tim said. “We always want the right tools in our toolbox to stand out from the crowd and that’s what we’ve done with the Paperless Parts and Plex integration.”
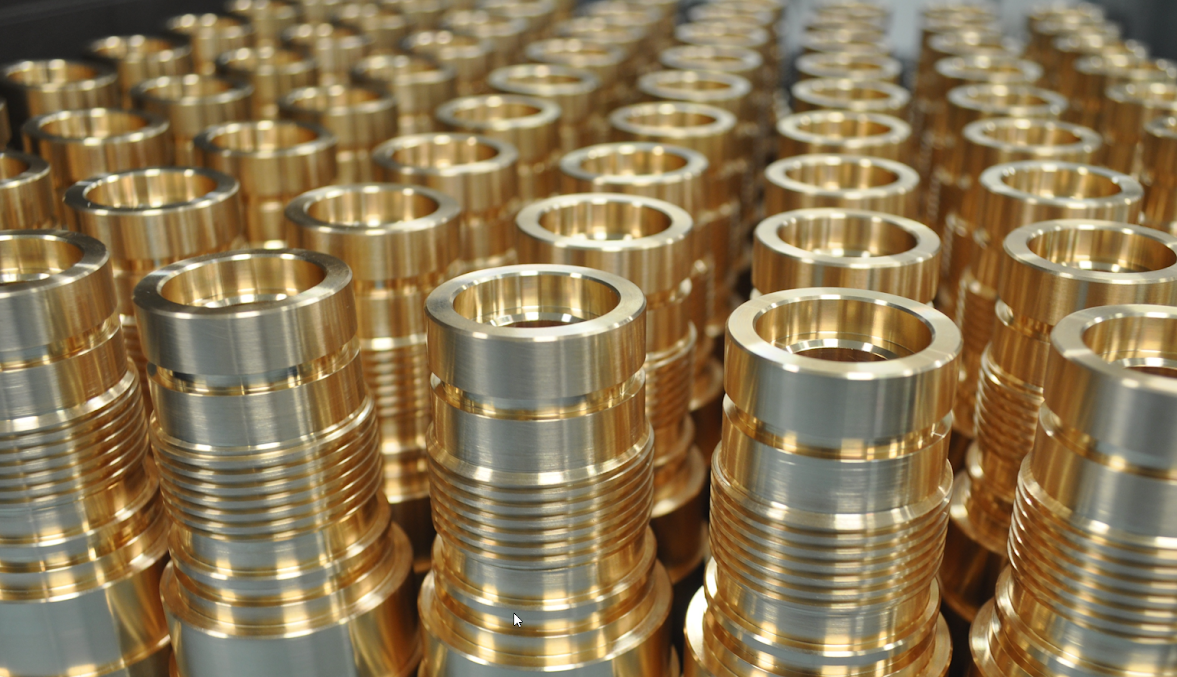
With the Paperless Parts and Plex integration, we have given our team the tools they need to be innovative and keep our company moving forward.