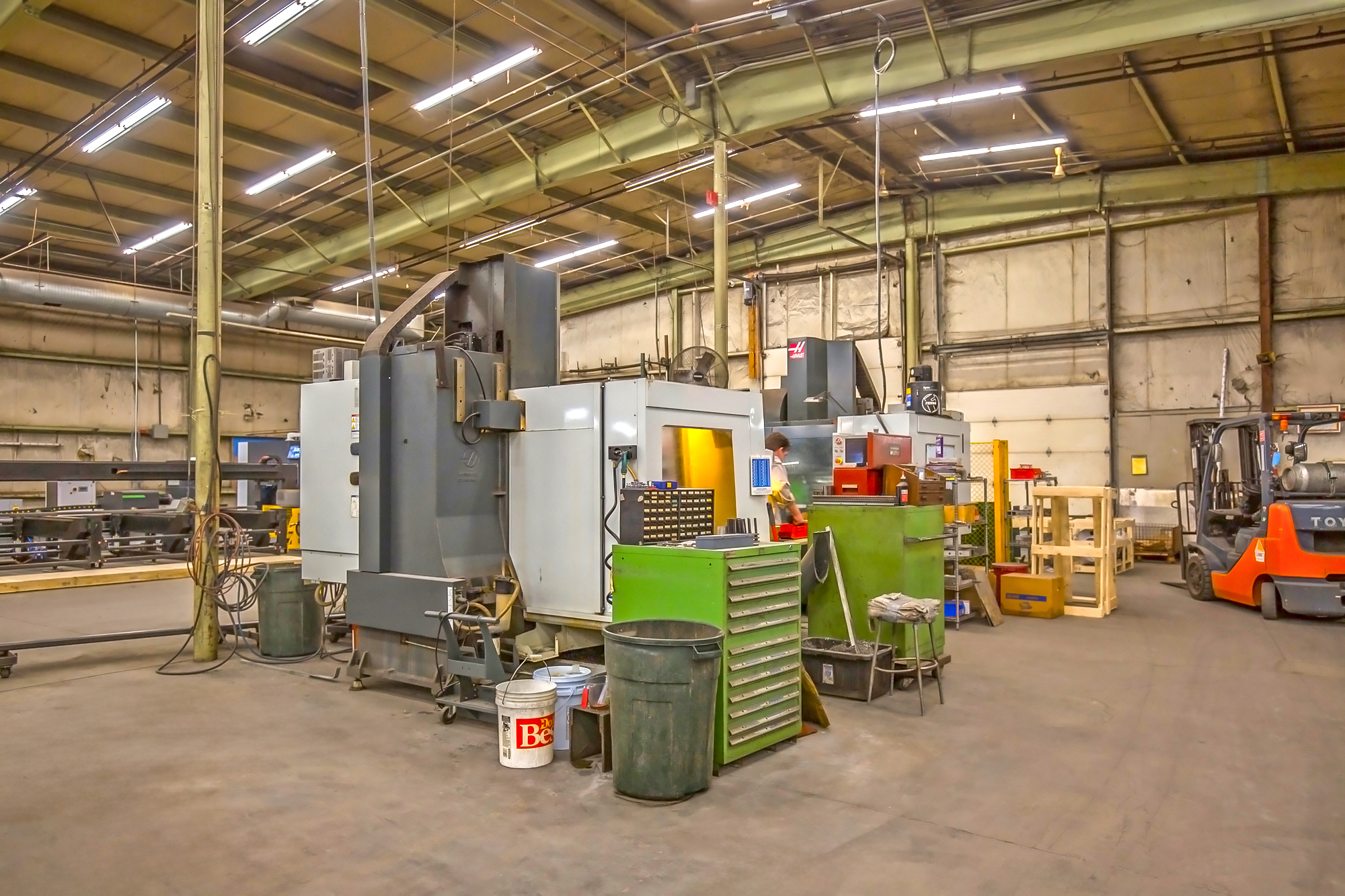
Motherhood and Manufacturing: How Shop Culture and Technology Impact Work-Life Balance
Wrapping up my last year of tech school, I was eager to learn and grow my manufacturing career. But with that excitement came a lot of uncertainty about breaking into a new industry.
I was lucky enough to land a role as a CNC operator at CAMM Metals, a family-owned job shop and leading manufacturer in East Windsor, CT. Walking into the interview, I felt the weight of my inexperience.
But Matt Soucie, the president, saw something in me that I hadn’t yet recognized in myself and offered me a part-time position while I continued my education.
Life threw me a curveball when I least expected it; I discovered I was pregnant! It was a joyful yet daunting realization: How would I balance motherhood with my new career? The shop was a 90-minute drive from our house, and my job required me to be physically at my machine.
When I told Matt the news, I was prepared for him to let me go. The commute was simply too much to take on with a newborn, and I had no idea how I would provide value remotely. But Matt’s response was, “We’ll figure this out.”
Forging a New Path
After thoughtful consideration, Matt offered me a position as CAMM Metals’ estimator, a critical function of the shop that Matt was previously handling on his own. I wasn’t sure I could handle it.
Luckily, CAMM Metals offers two key benefits that allowed me to step into the new estimating role while continuing to work from home:
1. A modern front-office technology stack
CAMM Metals prioritizes cloud-based technology for seamless connectivity between the front office and the shop floor. Using Paperless Parts’ quoting software, all I need to do my job is a device with an internet connection.
I can review our customers’ files, cost, nest, and price parts all within Paperless Parts. I can easily collaborate with my team through workflows and secure instant messaging. Then, I can send quotes to customers and follow up with them until an order is placed—all from my home office. Plus, Paperless Parts integrates seamlessly with Fulcrum, our ERP system, keeping me updated on shop floor activities in real-time.
Paperless Parts’ user-friendly interface and built-in training modules also allowed me to get up to speed quickly. With access to interactive videos and tutorials, I was able to master the program on my own (with help from Matt along the way!), even in the midst of sleepless nights and diaper changes.
CAMM Metals’ President Matt Soucie using the Paperless Parts platform.
2. A supportive culture
Matt fosters an inclusive and understanding environment at CAMM Metals. Whether through flexible work arrangements or simply being there to lend a listening ear, the support I’ve received from my colleagues and leadership has made all the difference. I felt it the moment I walked through the doors on my first day—being in a predominantly male industry, I anticipated being treated as “the new girl.” Instead, I was just treated as “the newbie;” everyone lent a hand to help me get up to speed with the utmost respect and support.
The forward-thinking culture at CAMM Metals allows me to navigate the challenges of parenthood without sacrificing my professional aspirations. And with each passing day, I grow more confident in my abilities, knowing that I have the technology and team behind me that will support me every step of the way.
Change can be uncomfortable. But I’ve learned that change isn’t something to be feared—it’s something to embrace. And today as I look to the future, I do so with far more excitement than uncertainty.
Want to see how Paperless Parts’ cloud-based platform can help empower estimators at your shop?
—
Amanda Rose is an estimator at CAMM Metals, Inc: a family-owned precision sheet metal fabrication company in East Windsor, CT.