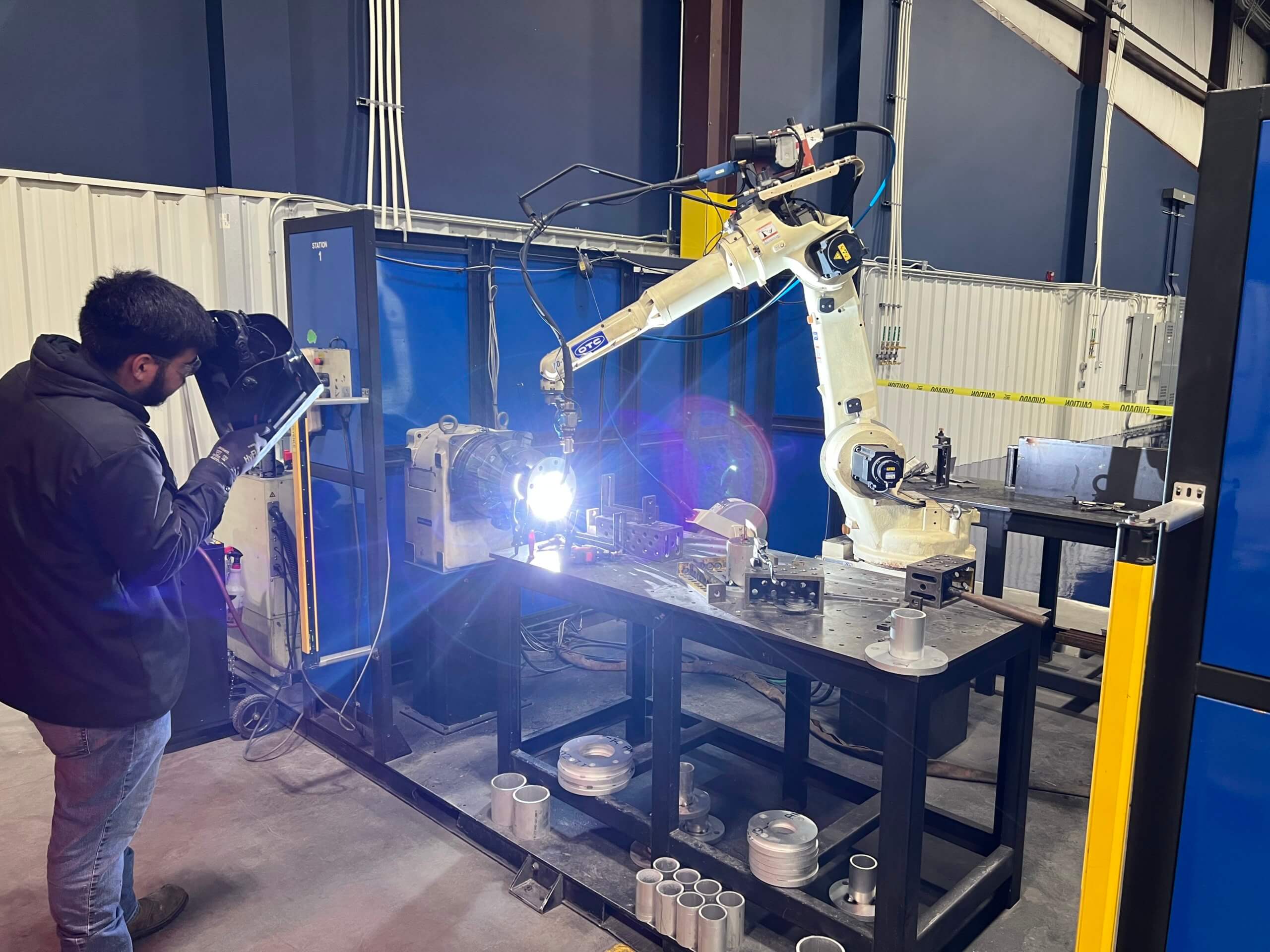
How to Incorporate Automation into Your Job Shop
As a leader in advanced metal fabrication, Ameritex is committed to leveraging the most innovative technology to make our customers’ products.
We believe incorporating automation and, eventually, artificial intelligence will help our organization run even more efficiently and effectively than it does today. We’ve experienced the benefits of automation not only on the shop floor, but also in our administrative office. And we know that implementing it in both places is key to a successful future in manufacturing.
Automating Our Shop Floor
We automate as much as we can on our shop floor. For example, our lasers and press brakes load and unload tooling and raw materials without human intervention. Robotic deburring and welding systems help us turn around parts faster.
Automating the shop floor allows for greater and more predictable capacity. Having machines that can load and unload themselves means fewer resources are required to cut parts. And we maximize our output by operating our equipment unattended overnight.
Automation can help fill the gaps caused by labor challenges, even when team headcount is reduced. We now need fewer employees with years of shop experience; instead, we can supplement and build our team with entry-level employees who can support production and learn more skills on the job.
Automating Our Administrative Office
Even if a shop floor is automated to the full extent, it will be hindered by an office that can’t keep up. Incorporating automation into administrative services is imperative if companies want to advance and meet growing demand.
At Ameritex, we integrate Paperless Parts’ automated quoting software with our ERP, E2, and the CADMAN software suite. We automate every possible part of the project, leaving only the more sensitive and highly detailed work to a small team of skilled professionals who make sure every project runs smoothly. Our team is dedicated to lean manufacturing practices, and these systems help us improve speed and efficiency without compromising quality.
In manufacturing, the money doesn’t come from office work—anything administrative is just overhead. Our revenue comes solely from fabricating parts, and automation helps us do that much more effectively.
4 Tips for Incorporating Automation in Your Shop
Automation is helping our business grow, and the data speaks for itself. In 2021, we produced 1,051,015 parts—up from 161,053 parts in 2015.
Are you ready to integrate more automated technology into your organization? Here are four tips to consider as you get started:
1. Simplify your processes
Automation is a tool designed to streamline workloads. To be effective, you’ll first need to audit your processes to identify areas where you can simplify. Ask yourself where automation could be helpful. Which tedious tasks could you replace? Where are your workers burning billable hours?
Investigate the processes you have in place, identify where you want to make upgrades, and decide how to incorporate automation. You may need to experiment to get it right.
2. Choose an automation champion
You might find that your team is hesitant about adopting new technologies. It’s crucial to have a tech-savvy individual to implement and evangelize the technology for the rest of the team.
Create a plan and choose an automation champion to lead the charge toward using new technology. The ideal person for this role will have comprehensive knowledge about the automation system and the right energy to build confidence among teammates (it might be you).
3. Communicate necessary information to customers
Automation does have limitations. Educate your team and, over time, your customers about your equipment so they understand the parameters of your capabilities. Let them know in advance if custom work requiring manual processing is more expensive and has long lead times.
Automation is supposed to make everyone’s life easier, so don’t complicate customer relations by holding back crucial production details.
4. Think about the long-term benefits
Shop leaders may be put off by the high price tag of automated technology, taking the stance that their teams can beat automated production times. Is this true? Can production teams win a race against automated systems?
Sometimes, but not always, and certainly not for long. While you could probably get an excellent crew to work faster than an automated line at the beginning of a project, your people will eventually need to take breaks, eat lunch, and go home to their families.
An automated system, on the other hand, will keep working 24/7 until the project ends. It’s steady and predictable. If you’re daunted by the upfront cost, remember that you’re investing in a consistent way of doing work, around the clock, all year long.
While the manufacturing industry has made massive strides in adopting automation over the last 10 years, we’ve only just begun to see what these technologies can do. If you want to compete with modern job shops, you’ll need to embrace automation on your shop floor and in your administrative office.
Once you identify how and where you can automate work, find a champion who can get your team excited about the new technology. The future of manufacturing is here—don’t miss it.
See how Paperless Parts can help automate your estimating and quoting process.
This article was written by Zack Fennell
__
Zack Fennell is the COO of Ameritex, a custom metal fabrication company in Willis and Conroe, Texas.