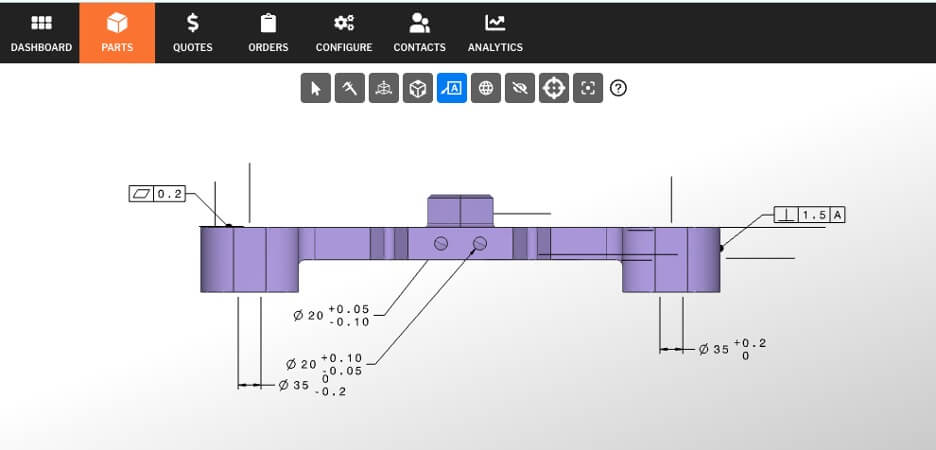
Bridging the Gap: How Paperless Parts’ New PMI Visibility is Empowering Our Users
During my time as a manufacturing engineer before Paperless Parts, I spent a lot of hours battling geometric dimensioning and tolerancing (GD&T) headaches.
I was the lead technical resource for a manufacturing cell that utilized a wide array of inhouse manufacturing processes, from assembly, to machining, forming, brazing, heat treat, EDM, NDT, and beyond. It was up to me to drive the technical vision for the cell in terms of process improvements (reducing costs, driving scrap, shortening cycle times) while introducing new technologies to help us achieve those goals.
Much of my time was spent interpreting prints and parts and trying to make critical decisions based on the information in front of me.
I was lucky enough to have a seat on our Siemens NX account that could view Product Manufacturing Information (PMI) on models if annotated. Since I was not working in NX every day, it was painfully slow and cumbersome for me to use. Rather than booting it up myself, I’d go bug a designer who might already have it open.
After walking across our entire shop, I’d tap someone (who was clearly busy) on the shoulder and ask them a question that required viewing the 3D model. This ate into both of our days more than it should have.
A New Era
To date, accessing PMI has required additional subscriptions to CAD software, putting this critical information effectively behind a paywall. With Paperless Parts, users can now extract and display PMI – dimensions, tolerances, parallelisms, datums, text annotations – directly in their browser.
Data is available from all files that can contain PMI, including STEP AP242, JT files, 3D PDFs, and native formats from platforms like SolidWorks, Catia, PTC Creo, and Siemens NX.
I’m fired up about this for a variety of reasons, but to name a few:
- We’ve taken PMI out from behind a hefty pay wall so shops can spend less money on software.
- Our customers (especially those in the aerospace industry whose market is competitive enough as it is) can turn quotes around faster by eliminating the time it would usually take to boot up CAD/CAM software.
- It bridges a major language barrier. Being able to exchange information that used to live on static drawings is critical in codifying and sharing tribal knowledge with manufacturers.
- Eliminating the need to manually cross-reference another screen with CAD/CAM software or an annotated 2D PDF file will reduce human error and catch mistakes before they happen.
- Viewing PMI within the context of a centralized quoting system allows shops to make informed decisions based on the model’s tolerances.
The pain points this enhancement eliminates are deep, and the benefits it provides will impact individuals’ mission-critical tasks. At the end of the day, greater accuracy and precision with faster quote turnaround time will positively impact the entire supply chain.
Why Tolerances Define Everything
Manufacturers call parts with tight tolerances, “quick to make, forever to inspect.”
How an engineer chooses to apply GD&T to their part design determines the manufacturing processes that can be used to produce a part.
For instance, if an engineer uses a true position tolerance of ± 0.250, I could generate that feature with a hand drill. However, if the positional tolerance of that hole is ± 0.0002, you might be forced onto a jig grinding machine. The cost difference associated between those two technologies is staggering (the latter is a very, very expensive part).
Tolerances also determine which inspection tech can be used. Will you use a tape measurer? Caliper? Micrometer? CMM? Being able to view tolerances within Paperless Parts helps you make more informed pricing decisions from the very beginning of the quote to cash process.
Looking Ahead
Aerospace designers are already doing it, but more and more industries are beginning to share PMI on their 3D models. Our customers will be prepared to quote their parts faster and more accurately.
If I was still in charge of adopting new technologies to optimize my previous shop’s processes, the first thing I’d do is get Paperless Parts up and running. As I tell the Paperless Parts customers I work with now, I’m so excited to see the evolution of Paperless Parts’ PMI offering. But we move fast, so don’t get too comfortable – we’re just getting started.
Want to learn about all recent enhancements we’ve made to our Part Viewer?
—
Alex Renner joined the Paperless Parts team earlier this year after working in multiple supply chain roles at GE Aviation starting in 2014. As an Implementation Project Manager, Alex helps Paperless Parts customers leverage our platform to drive efficiencies, optimize resources, and win more work.