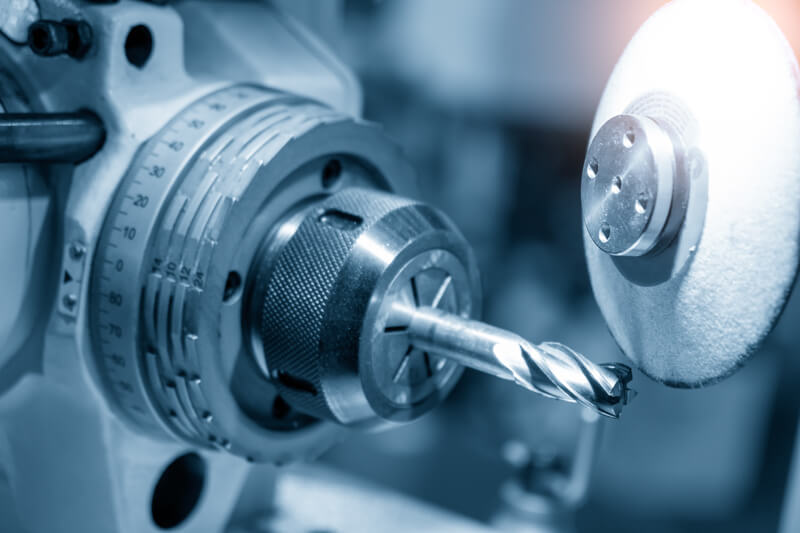
How Does Industry 4.0 Affect CNC Machining?
Industry 4.0 aims to revamp professional responsibilities and manufacturing techniques to enable large-scale developments in the industry. It concentrates more on improving the industrial ecosystem through automation integrated with the application of versatile technologies and intelligent solutions like AI, big data, cloud computing, ML, and IoT.
Innovation must essentially be merged with CNC machining to transform the industry into one that is more competent in the present and the forthcoming market dynamics. Like other sectors, the machining sector is expanding quickly in the direction of a better, more integrated, and concise network system to supplant obsolete and inefficient ones that restrict large data transmission. The advantages of Industry 4.0 for CNC machining are now trending issues in the industry.
What Does Industry 4.0 Imply?
Industry 4.0, popularly known as the “smart industry,” emphasizes automation and technology application in industrial processes. The partial substitution of automation systems for human cognitive functions is the prominent element of this process. The relationship between humans and technology is advancing nowadays with the advent of the internet and the quick emergence of the Internet of Things. The wireless transmission and data collection are the main components of this process.
By automating numerous industrial procedures, these new-age technologies help drive digital transformation and build “smart” production facilities. As a result of data sharing and communication between systems, turnaround times get shortened, and overall manufacturing expenses get reduced.
Understanding the Influence of Industry 4.0 on CNC Machining
Here are some of the most prominent ways in which CNC machining can reap the benefits of Industry 4.0 implementation:
1. Enabling real-time quality assurance
Manufacturing businesses always employ a quality assurance procedure to inspect components or finished products for flaws or minor defects. But several of these procedures have the drawback of delaying manufacturing.
Real-time QA techniques like automated virtual metering (AVM) systems, made possible by Industry 4.0 and associated technologies, will transform this practice. In essence, data on certain scenarios, performance, and conditions are gathered and merged with the data about machinery and procedures. It provides a more thorough picture of undergoing operations and offers aspects of quality control that could be inspected in real-time.
2. Enhanced energy savings and operational efficiency
Equipment and machine tools demand a lot of power to operate with utmost efficiency. Even when they are turned off and are only on standby, they still consume a lot of energy. We can control resource utilization better using Industry 4.0 technologies.
Operations can be made more effective by leveraging data gathered by Industrial Internet of Things (IIoT) sensors, CNC machining quote software, and systems deployed on CNC machines. We can install smart meters to efficiently manage the flow of energy. Moreover, the machinery can be automated or powered adequately to lessen the environmental effects and supplies.
3. Achieving better operational reliability
Conventional manufacturing methods and equipment aren’t always dependable as labor, production, and maintenance costs all go up during downtime. But Industry 4.0 offers a solution in the form of modern, tech-enabled preventive maintenance systems. Thanks to the solutions offered, equipment maintenance teams can effectively anticipate and plan for potential malfunctions or defects with real-time data streaming. This way, before routine processes halt, emerging issues can be identified and corrected quickly.
Furthermore, with advancements in big data solutions, we can now create predictive machine learning models and algorithms capable of spotting future breakdown spots. Due to this, the CNC router and other equipment can operate continuously without breakdowns, more efficiently than before.
4. Establishing effective collaboration between humans and machines
It takes more than just better performance and consistent operation to upgrade the current generation of machinery and production facilities. The same is true of the man-machine interaction standards. Implementation of Industry 4.0 implies that the majority of workers leverage collaborative robots and technology to complete daily production operations.
Since humans, machinery, and robotic systems can all work together in a safe and controlled atmosphere, future manufacturing and production facilities are bound to be remarkably efficient. The man-machine interaction needs to be greatly improved to accomplish this goal. Remote operation and immediate command transmission will be possible for technicians irrespective of the operator’s location. Also, the monitoring system can offer them real-time notifications and insights. All of it can be possible thanks to Industry 4.0.
Conclusion
For manufacturers and CNC machining facilities, adopting data and integrating with Industry 4.0 technologies can result in more productive and operationally efficient processes. Despite the workforce’s increasing obsolescence, manufacturing businesses continue to look for new technologies to improve the efficiency of their manufacturing operations.
But at the same time, it is essential to prioritize training and development when embracing this new digital shift to Industry 4.0 technologies so that existing personnel get the space to migrate and adapt more smoothly. Due to the manual operation and supervision requirements of these modern automated systems, training staff will be necessary to undertake substantial changes and system migrations.
Learn how Paperless Parts can help you quote CNC parts faster today.
–
Peter Jacobs is the Director of Marketing at CNC Masters, supplier of CNC mills, milling machines, and CNC lathes.