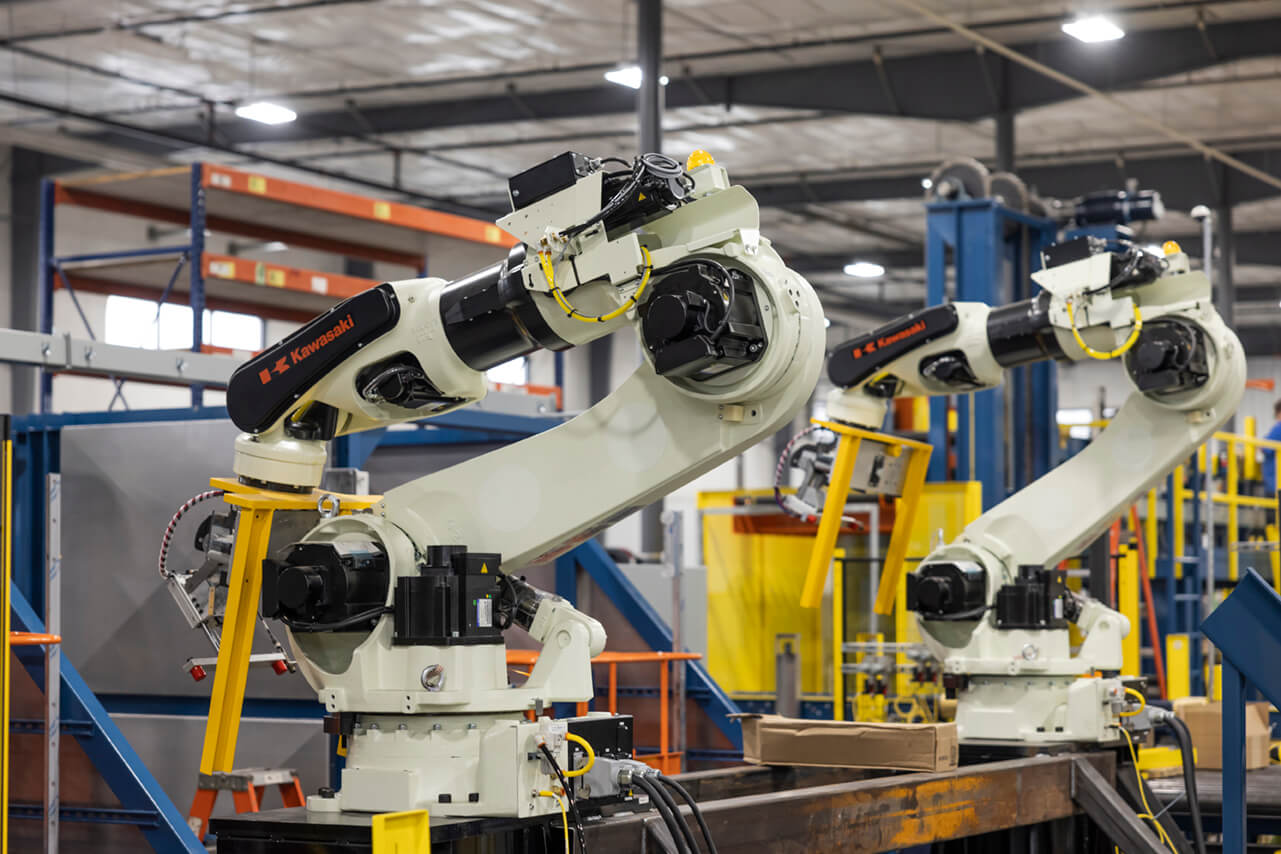
How Modern Technology is Making Small Manufacturing Businesses More Competitive
98.6% of American manufacturing businesses are small businesses, meaning they have 500 employees or less. Even more interesting 75% of those small businesses have less than 20 employees. For too long, these scrappy, entrepreneurial, often generational creators and builders have lacked equitable access to the same technologies and modern solutions as larger, enterprise-level manufacturing businesses.
Modern technology – everything from AI to machining software – is leveling the playing field. Automation allows small businesses to adapt and solve problems in ways that have historically been out of reach.
Take for example robot and cobot arms: while they have been around for decades, if you’re a smaller shop you may not have a full-time robotics or controls engineer available to design, develop, and support that arm.
But times are changing – AI and machine learning has made robotic programming simplified for its end user. You no longer need experienced engineers to set up a job; now, a robot working alongside vision systems can identify many components on the field just by a person teaching it “good” or “bad.”
The simplicity in machine tending for robots is also on the rise. With many machine shops having a hard time finding skilled operators’ companies can leverage robotics in lights out and reduced labor demand operations.
We are also seeing machining software becoming easier to use and more affordable. Improvements are not just on the production floor but in the office as well. By using software like Paperless Parts, it allows less experienced employees to step in and estimate the cost of jobs so that they can return quotes faster and win more work.
With the ability to be more productive than ever, small manufacturing companies are able to compete on a global scale.
Why We Need Small American Manufacturers to Thrive
Manufacturing is the backbone of the U.S. economy. It accounts for 8% of our country’s workforce and 11% of the GDP. Luckily, reshoring is happening at a record-setting pace; it’s more expensive, slow, and risky to manufacture and ship products overseas than it is to make products in the U.S.
However, being located in Michigan, we are still feeling the effects of the chip crisis every day as many are. There is an unprecedented opportunity for domestic manufacturers to help fulfill the demand for critical parts in this country.
We must also consider the effects of The Great Resignation: during the pandemic, around 3% of manufacturing jobs were unfulfilled. By 2022, that reached 7%. As a result of this year-and-a-half long movement, the U.S. has lost $92 billion in manufacturing output. This directly contributes to our inability to fulfill critical work.
5 Ways Automation & Technology is Empowering Small Manufacturing Businesses
So how do we ensure that the majority of our workforce can do more with what they have? Automation and modern technology provide small to medium-sized businesses with:
1. Added Flexibility
Many small-medium sized manufacturing businesses do small production/high-sku variability work. Today, automated solutions are designed around flexibility; cobots can do a lot of different tasks, and AI is flexible in how it’s programmed. Modern technology enables small businesses to work faster and smarter because it’s equipped to handle high variability work.
2. Faster Decision-Making
“The Connected Worker” is describes employees that have devices in their hand or wearable devices that make it easy for them to quickly make decisions. Let’s say they have their digital work instructions on their cell phone. VR heads-up displays are becoming more popular on the floor. There are also wearable devices that work as a bar code reader for people to scan parts or do inventory checks. Having remote, wireless, instantaneous access to this information yields greater productivity.
3. Process Efficiency
Automation enables people; it doesn’t replace them. When humans work alongside robots, they can do more of what they love. Instead of walking miles a day around the floor, operators can offload that task to autonomous mobile robots (AMRs) and focus on what they’re good at: selective picking.
4. Deeper Data Insights
Too often, downtime is the only productivity metric manufacturers focus on. But modern technology is able to report on numerous other variables that can help you work more efficiently. Having access to data analytics shows you what’s happening on the shop floor: What is your Overall Equipment Effectiveness (OEE) and better term productivity? What jobs are your operators assigned for the day? Taking a Total Productive Maintenance (TPM) approach helps you prioritize jobs and anticipate hurdles before you dive into completing the dozens of orders that may be on your plate that day.
5. Skills Gap Relief
These days, end users can pick up a robot and program it with far less risk than they could have twenty years ago. If modern technology is a resource employees at small businesses can leverage, younger generations that are technologically-savvy and highly independent in how they solve problems can provide greater value. The downstream impacts? Employees feel a greater sense of purpose and responsibility and want to stick around longer.
Pulled from a recent presentation given by Jake at IndustryWeek’s Executive Summit.
Springing Into Action
So how can small and medium-sized manufacturing businesses get on a path towards technological innovation?
- Get comfortable leveraging local organizations and state-funded programs for support. In every state, there is a Manufacturing Extension Partnership (MEP) program – take advantage of yours.
- Get involved with local colleges and universities. Turn to them for not only recruiting purposes, but try to understand what they’re teaching: where are they in terms of robotics? Which machining software programs are they training people on? Stay in the loop so you can stay ahead of the curve.
At the end of the day, if you’re not actively engaging in conversation to better leverage resources available to you, you’re completely missing out.
“Automation” can be a scary word in manufacturing. But I can’t say it enough: automation doesn’t replace people. Automation can lift the burden of menial, manual, time-consuming tasks that eat into the day and create unnecessary constraints on your performance. It affords you time to do more of what you love.
Modern technology has gone from being a secret weapon to a bare minimum requirement for successful manufacturers. I encourage everyone to embrace Industry 4.0 with open arms (and maybe a robotic one, too).
Related Content
Learn practical advice for filling the skills gap with modern technology, attracting top talent, and retaining your existing workforce in this roundtable discussion featuring 3 savvy shop owners.
—
Jake “The Manufacturing Millennial” Hall is a passionate advocate for manufacturing, automation, digital transformation, and skilled trades. With nearly 50 million views on his content, Jake creates awareness within and outside of our sector to fuel innovative ideas and attract the next generation workforce. Follow The Manufacturing Millennial on LinkedIn here.