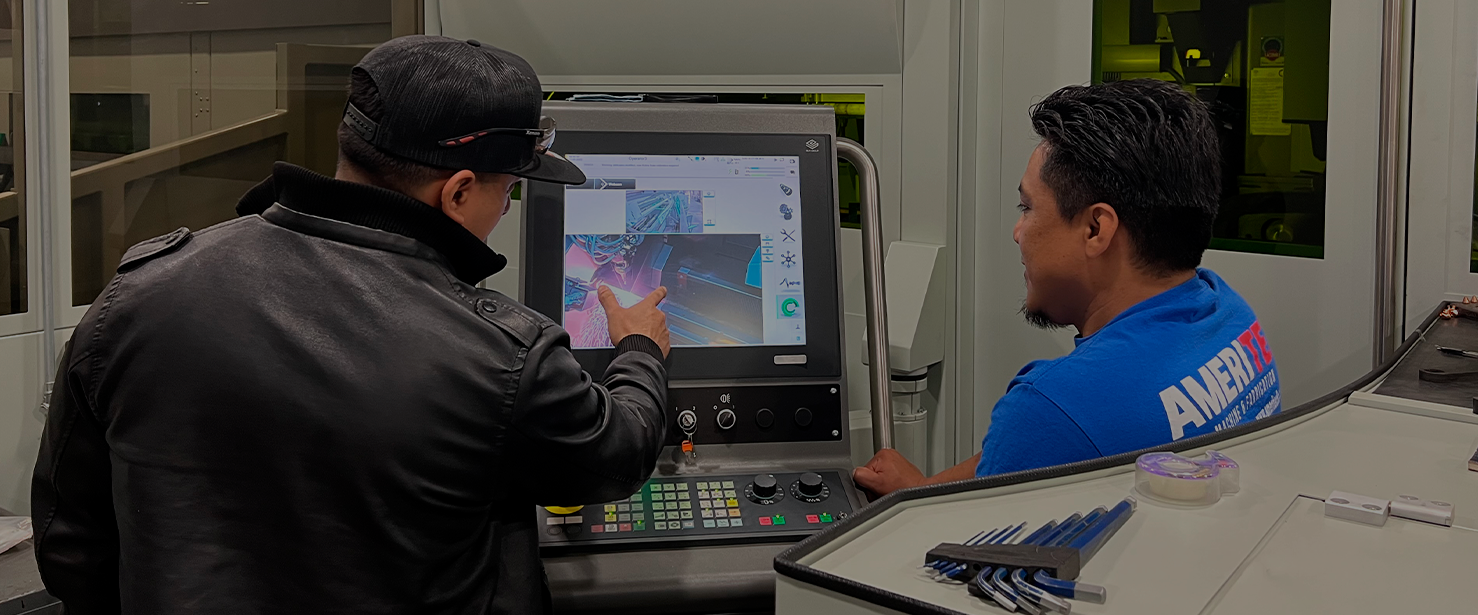
Here’s Why The Perfect Machining Run-Time Doesn’t Exist
Paperless Parts has invested millions of dollars in R&D, written countless lines of code, and secured multiple patents. We’re embedding cutting-edge machine learning and AI technology into our software, ensuring our customers are armed with the most powerful quoting solution on the market.
And yet, we still get this question all the time: “How accurately does Paperless Parts predict machining run-times?”
It’s a question we both love and hate. We love it because it means our customers are thinking strategically about how to cost specific jobs and probably looking for a better answer than their current process. We hate it because, if we’re being honest, the answer is that the “perfect” run-time simply does not exist—especially when you’re at the quote stage of a project.
There are just too many variables involved, and those variables change between the time you quote a project and when you actually start making a part. Oftentimes they change between part runs on different days.
When it comes to machining run times, here are six variables to keep in mind:
6 Variables for Machining Run-Times Probably Not Precisely Known at Time of Quote
1. Size and availability of the raw material
At the time of quote, there are a few material unknowns that may dramatically affect run-times because of their impact on programming:
- What is the stock size?
- Will it be cut near net shape or rectilinear from bar or plate?
- What different options are available from the metal supplier now vs. what will be available when the order is won and placed?
- Which supplier will you actually buy from?
2. Fixturing
Will the raw stock be clamped in a vise? Or will soft jaws be used? Or maybe a custom fixture? How many parts will be fixtured at once? Different programmers and operators might tackle the same solution in different ways, as an example possibly reusing existing soft jaws that require a slight adaptation. Different machining centers may also have different fixturing options. Maybe you can use a jig plate. Fixturing has so many options and opportunities for different flavors to be used.
3. Programming
Each programmer has their own way of doing things based on their experience, and that often creates variability in run-times. We even see variations from the same programmers based on variables such as time of day: if it’s midday on a Tuesday, the programmer might be more focused than on a Friday morning after a late Thursday night out.
4. Tooling
An aspect of programming or perhaps the actual shop situation when the parts hit the floor, tooling choices can impact Material Removal Rates. Each programmer has different tooling preferences and also different levels of willingness to investigate or wait for alternative, faster MRR tooling solutions. Will a new or used end mill be used? And then reality happens: the end mill programmed is not available and a substitution must be made to keep the job moving.
5. Operator/Machinist
Just as there is variability among programmers, different operators may run the same program on the same machine differently. They might lower the speeds and/or feeds, affecting the time it takes to complete the part.
6. Machining Center
The machine used to make the part can also impact quoted run-times. Maybe the Haas machine is already being used, so you have to use the Mazak machining center at a higher hourly rate. I saw older Haas VF2s take longer to run the exact same program compared to a new Haas VF2. It’s the “same” machine, but the run-time is significantly different.
Bottom line: The goal isn’t to get a perfect run-time (you can’t). The goal is—as quickly as possible—to get a “close enough” run-time; one that protects the shop financially AND gets the quote returned quickly.
The way I’ve always thought about it is that you want to come up with a realistic run-time. One that you are confident that is most likely within a bounded range. A run-time that, on the low end, will not ship dollar bills out the door with each part and on the high end, will still keep you competitive.
You almost always win the jobs you price too low and never win the ones you price too high.
Paperless Parts was developed to help you get to a realistic machining run-time quickly. The faster you can confidently get to this bounded range run-time, the faster you can provide the quote. This gives you more time for the next quote in your queue, as well as more time for back and forth with the customer to win the job. And data shows that the faster the quote is returned, the higher the win rate!
Paperless Parts isn’t chasing the dream of a perfect run-time. Rather, we are all in on helping you—with the fewest possible clicks and minutes—get to a bounded range that is as tight and accurate as possible.
Seasoned estimators know their shops, their machines, their programmers and their operators. That’s why Paperless Parts is designed to be so customizable. During onboarding, our team works hand in hand with you to put tribal knowledge into our software, making it reflect how you actually do business. The software’s automated part file analysis flags critical information like process-specific features (holes/pockets/3D machining), provides manufacturability warnings, and instantly calculates volume removal—all of which quickly help dial in that bounded range run-time.
When the intuition of the seasoned estimator becomes part of your quoting process, quoting becomes more accessible to junior estimators and helps drive overall quoting consistency across the team.
Want to see how it works? Schedule a custom demo (key word custom) with one of our experts today.
—
Jay Jacobs has a passion for custom part manufacturing and has been immersed in the job shop community since 1987, buying his first 3D Printer in 1989. Jay has sold to job shops, worked for job shops, owned job shops and been a customer of job shops. Processes he has been involved with include machining, sheet metal, injection molding, 3D printing/additive manufacturing, metal and plastic castings, springs and stampings. As the former founder and owner of RAPID, he and his team grew from five to over three-hundred strong while creating the world’s largest sheet metal prototype company. Before RAPID was acquired by ProtoLabs in 2017, they were quoting over 100,000 unique part numbers and manufacturing over 30,000 unique part numbers per year out of facilities in Nashua, NH. eRAPID. Jay is a Co-Founder and Chairman of the Board at Paperless Parts.
—
This article was updated on October 1st 2024.