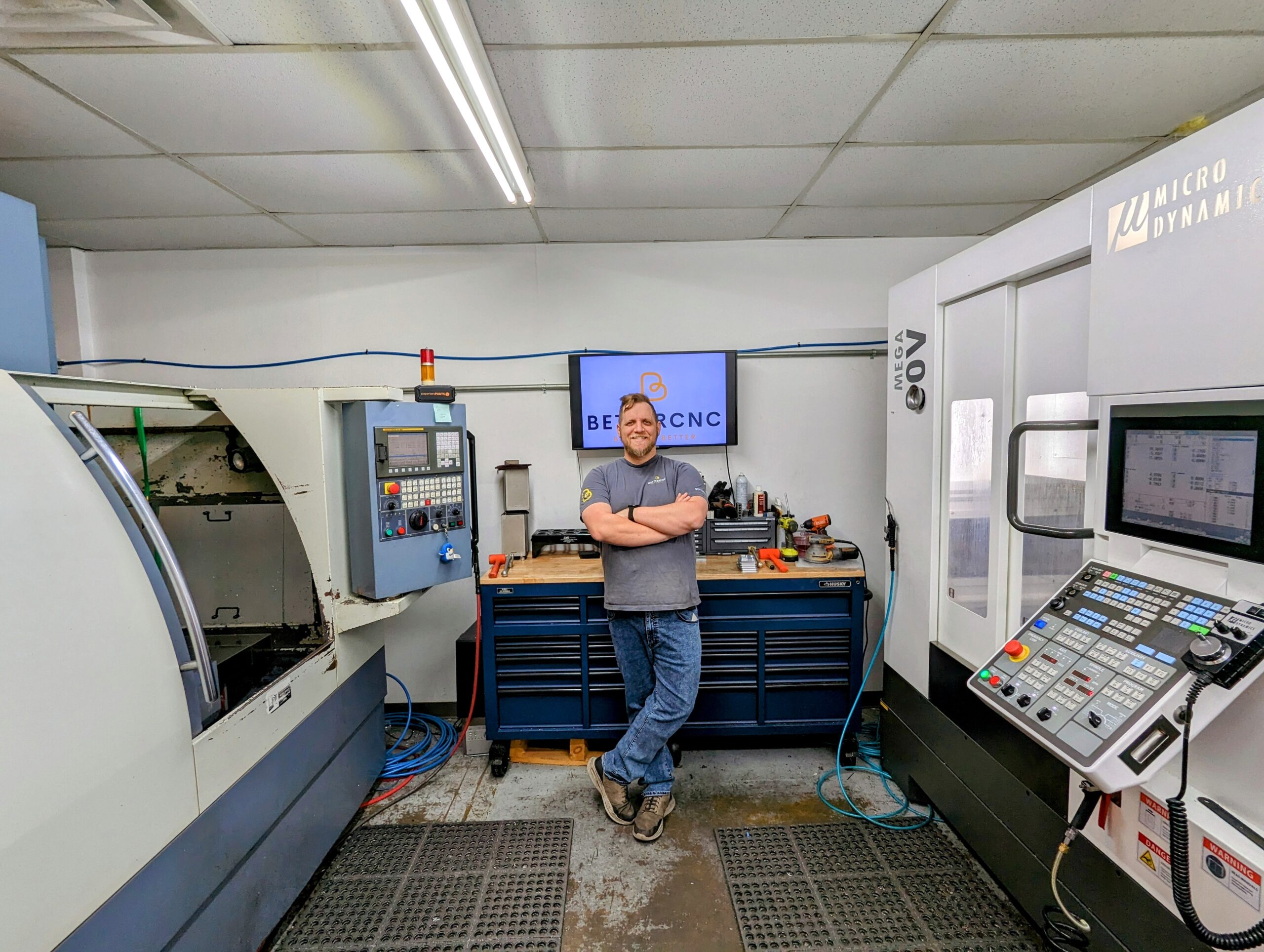
From Prototype to Perfection: How to Commit to Continuous Improvement in Your Shop
Growing up in my dad’s machine shop, I learned the value of incremental improvements. He and my grandfather lived by the mindset that to start a new company, you don’t have to have anything new or innovative—you just need to do something just a little bit better than everyone else. That stuck with me and later became the foundation of my approach to business.
When I first started my journey with BetterCNC, I knew I wanted to create a company that embodied the principles of continual improvement and progress. The name itself, “BetterCNC,” reflects this vision.
In the early days of BetterCNC, when it was just me running the show, I was so focused on pushing out products and meeting the demands of my customers that certain areas of the shop were falling behind. I thought keeping my nose to the ground was the only way to grow, but it was actually holding me back.
Raising your Gaze
In the pursuit of improvement, you may often find yourself deeply engrossed in your work. But as a result, things like efficiency, organization, repeatability, and consistency begin to suffer.
At BetterCNC, I am constantly forcing myself to make the temporarily uncomfortable shift to work on my business instead of in it. Here are the key areas I’ve been focusing on:
Top-Notch Tooling
One aspect of our continuous improvement efforts lies in our approach to tooling. In many machine shops I’ve previously worked at, budget tools were the norm. However, I decided to experiment with higher-end tooling and sought guidance from representatives of different companies.
The results were astounding. By using superior tools, we’ve achieved significant time savings, increased machining speeds, and extended tool lifespans. Additionally, our CAM software’s tool library enables us to maintain uniformity and leverage the best available speeds for each tool we use. I firmly believe in utilizing every resource to its fullest potential.
Equipment Upgrades
Investing in new machinery has also been a critical part of our improvement journey. I am proud to have acquired a state-of-the-art machine, the Microdynamics Mega 30-V, which has garnered attention from tool representatives eager to demonstrate their products on our machine.
Looking ahead, I plan to replace my 2005 Leadwell 3-axis milling machine with a brand new Micro Dynamics 40-V next year. This commitment to upgrading our equipment ensures that we stay at the forefront of technology and maintain our competitive edge.
Expanding our Footprint
Originally, I signed a two-year lease on our current facility. But we outgrew the space within eight months. Next March, we will be relocating to a larger facility where we’ll incorporate a 5-axis machine, also from Microdynamics.
Our long-term goal involves a series of strategic moves until we find our final spot—a process that will span 3-5 years. With each transition, we aim to optimize our operations and create an environment conducive to growth and innovation.
Investing in (the Right) Software
One of my key priorities has been developing our very own ERP system. By building a custom solution for our needs, we’ve been able to streamline our operations, enhance communication, and optimize our workflow. This initiative is an ongoing project that ensures we are continually evolving and adapting to meet the needs of our growing business.
We also made the decision to invest in Paperless Parts two years ago. Paperless Parts is highly customized to our unique machine shop’s needs, and it’s revolutionized our quoting process; we generate and send out quotes with remarkable speed and efficiency, and are able to handle a larger volume of requests, supporting our business growth objectives. The built-in analytics allow us to make data-driven decisions that help us drive better margins and customer satisfaction.
Certifications
Obtaining our ISO 9000 certification later this year is another milestone on our journey of improvement. This certification will provide a framework for integrating continuous improvement into everything we do.
Long term, my aim is to embed the mindset of continual improvement into all of our processes and procedures to protect the longevity of our business.
“Shooting Yourself in the Foot”
Sometimes we have to shoot ourselves in the foot to become stronger. Before you call me crazy, let me explain what I mean by that.
When I first ventured into production planning, it was at a machine shop that focused solely on prototyping, and at the time, our on-time delivery (OTD) stood at a discouraging 30-50%. Determined to make a change, I developed a comprehensive planning system.
However, in the first month and a half of implementing this new approach, our OTD percentage actually plummeted even further. It felt like we’d shot ourselves in the foot.
Undeterred, we persisted, and the result was remarkable. Our OTD rate soared to an impressive 80-90%, becoming the new standard for us. Although the initial setback caused some discomfort, the overall improvement we achieved after learning from our mistakes was substantial and has transformed our business.
The Ever-Evolving Path to Success
The importance of continually improving cannot be overstated—especially for business owners and leaders. Throughout my career, I have witnessed many instances where companies hit a wall because they became complacent.
By allocating even a small portion of our time to refining our processes and workflows, we unlock significant time savings and efficiencies. Deliberately slowing down can actually yield substantial gains on the backend, whether you’re reducing cycle times, creating time to take a vacation, or boosting profit margins enough to hire a new employee.
And in cases where the expected improvements don’t materialize, the journey itself remains invaluable. Every attempt at improvement—regardless of the outcome—offers valuable lessons and insights that contribute to our personal and professional growth.
Commitment to improvement is never wasted, as it fosters a culture of learning and adaptation that can propel us forward in unforeseen ways. Ultimately, it’s the unwavering dedication to improvement that not only shapes our present, but paves the way for a brighter and more successful future.
Prefer to hear Jesse’s story in podcast form? Tune in to his recent episode of “The Job Shop Show.”
—
Jesse is the owner of BetterCNC, a CNC machine shop in Plano, TX, which he founded in January of 2021. From the moment of first contact with BetterCNC through shipping and beyond, Jesse and his team want to provide a better experience. Jesse is passionate about his work, having been raised to be a hard worker that never settles. One of his main goals in life is go learn everything he possibly can. To connect with Jesse on LinkedIn, click here.