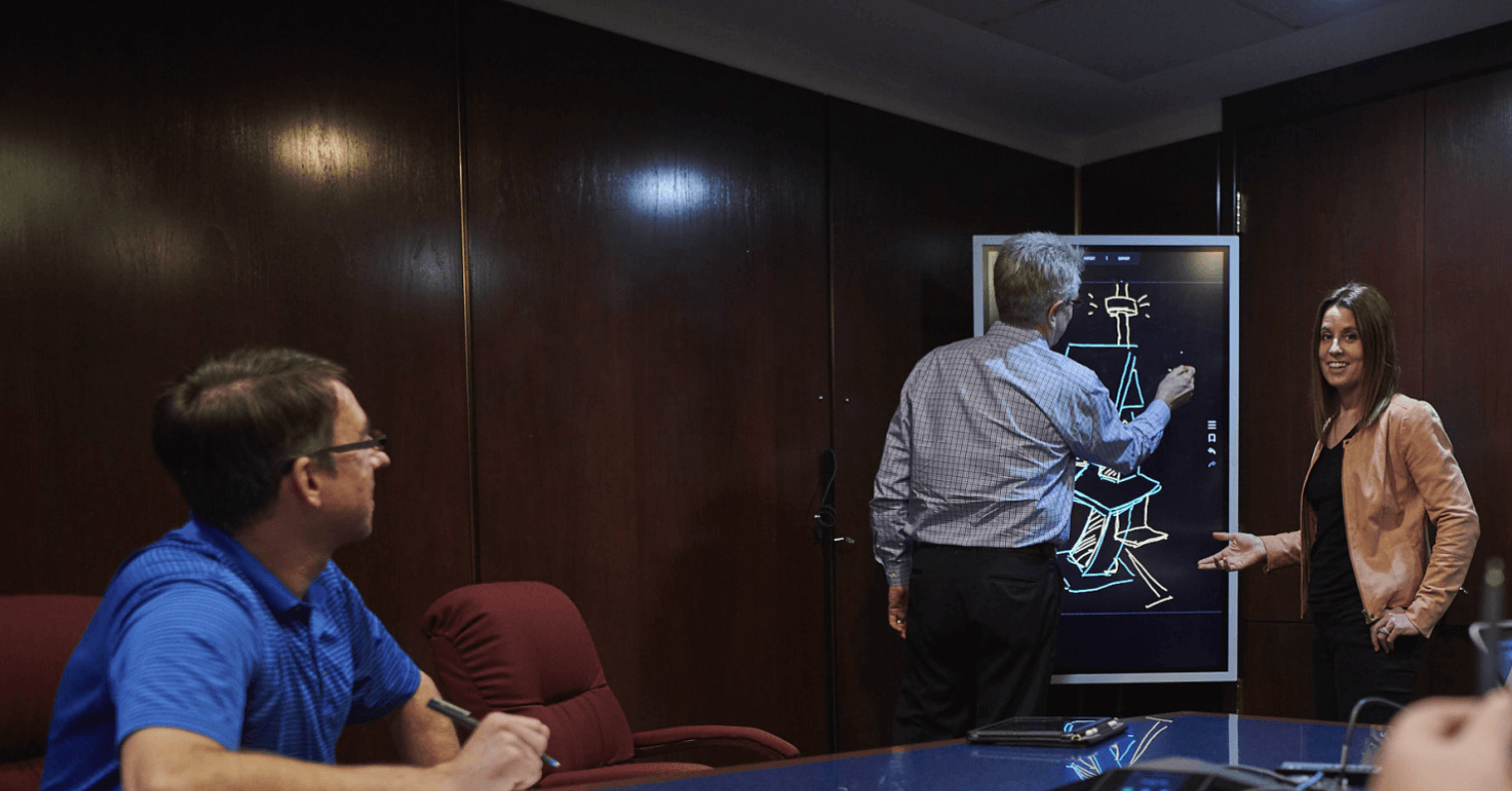
6 Tips for Facilitating Digital Transformation in Manufacturing
In life as with organizations, I subscribe to the truism that rigid objects break and flexible objects bend. I find that it’s better to remain flexible when contemplating change than to dig in and resist, and yet, our industry has a history of resisting change, especially when it comes to adopting new technologies.
The problem is that if we allow ourselves (and our employees) to adopt rigid thinking regarding skills and capabilities, we cannot bend, stretch, and grow without the risk of breaking.
Competitive companies are embracing Industry 4.0, implementing tech strategies, and integrating groundbreaking, innovative solutions on the shop floor and in their front offices.
As leaders, we face a unique challenge: How do we convince our employees and, in some cases, peers in leadership, to stretch themselves? How do we encourage our teams to embrace digital transformation instead of resisting it?
6 Ways to Make Digital Transformation Easier
I recently faced my own challenges with digital transformation at my company, Nu-Way, when we decided to implement quoting software Paperless Parts. Not all of our estimating and engineering team members saw the benefit of adopting a new, digital approach to quoting.
As the leader of these groups, I could simply issue a directive: “We’re implementing this software, period,” and consider the case closed. However, that’s not how I choose to lead.
Instead, I’ve been looking for ways to make this transition a win-win for the company and for our team. These strategies have made my conversations, and our transition to digital quoting, a little easier:
1. Make personal connections
When teammates are hesitant about adopting new tools because they are resistant to change or don’t see the relevance in their roles, I make a personal connection. I explain how the software will—in time—improve their job or their colleague’s job and why that matters.
Even when an employee doesn’t directly interact with the software, they can appreciate something that makes their colleague’s job easier.
2. Address the learning curve
If digital transformation were easy, everyone would have done it already. I acknowledge that learning new systems takes time and that integration of these new tools and practices takes time and is an ongoing process. This approach helps folks adopt a “beginner’s mindset” and shows them that they aren’t expected to know everything about the software on day one.
3. Be patient and ask for patience
I commit to being patient with my team as they get up to speed on the new tech, and I ask them to be patient as we ramp up the software. I encourage employees to withhold judgment until we’ve fully integrated the system and our team has been trained to use it effectively.
Jim leading a team meeting at Nu-Way Industries.
4. Request technology trust
To give the new tech a fighting chance, people have to trust it and use it as it’s intended. If my team goes into the software and overrides the automation that we’ve carefully set up, they’ll never experience the system’s true capabilities nor will we have the opportunity to tune the system to generate better results.
5. Discuss mindset
When there’s pushback against learning something new, the resistance usually isn’t about the new thing itself but the effort it takes to learn it and because something familiar and known is being replaced with something unknown.
If folks feel insecure about learning a new system, I acknowledge that they are excellent at what they currently do and encourage them to embrace the potential for learning new skills.
I also ask them to consider the benefits of expanding their knowledge. The more skills you acquire, the stronger you are as an individual and a professional.
6. Promote benefits
To obtain buy-in from my team, I tout the benefits of new systems.
For example, I discuss the ubiquitous access that Paperless Parts quoting software provides us. Team members can get into the system from any computer and aren’t restricted to workstations here at work, but remind them that work can be done anywhere. Paperless Parts is also highly customizable, which empowers us to adopt and implement the tools quickly and see fast results. Also, the ability to customize the software makes it future-proof. We can readily modify it as our business evolves, so it remains relevant.
Meet Objections with Realistic Assurance
Some team members may still object to adopting new technologies. The most common concerns I’ve heard are about data storage and internet outages.
Skeptics ask, “Where’s your data? Is it secure?” and “What happens if the internet goes down?”
I understand these fears, but I try to remain realistic and reassure my team that we can handle a catastrophe. I remind them that the internet is a utility in today’s world, just like electricity. It’s a mainstay in our daily lives. The threat of the internet “going away” isn’t realistic anymore, and if it “goes down,” that will be a temporary problem we can manage just like we do when the power goes out.
As for data breaches, cloud-based digital data storage systems are far more secure than local storage or paper files that could vanish due to a break-in, fire, or flood. There are risks with every data storage method, but I believe a digital cloud solution is the least risky option.
The Time is Now for Digital Transformation
If you’re contemplating digital transformation, now is the time to do it. Your competitors have already gotten started.
To set yourself and your company up for success, keep two considerations in mind:
1. Use the technology as it’s intended. When implementing new digital tools, there’s a tendency to start slowly, trying to recreate current operations with new tech. Don’t. The technology was designed to improve upon existing systems and workflows. You’ll miss out on the tool’s full potential if you place too many restrictions on it. Paperless Parts in particular is a highly customizable toolset that really is only limited by your imagination and willingness to invest the time in making it your own.
2. Build a forward-thinking culture. Embrace taking chances and calculated risks. By demonstrating your openness to change, you’ll influence your company culture and make it easier to drive digital transformation.
Industry 4.0 is upon us. If we want to win business and grow, we must get on board with the digital era.
__
James Fitch is the Vice President of Engineering at Nu-Way Industries, Inc., a leader in designing and fabricating precision metal products serving many industries worldwide. With a manufacturing career spanning five decades, James oversees Estimating, the Product Development Group, the Manufacturing Engineering Group, and the Prototype Shop from Nu-Way’s headquarters in Des Plaines, Illinois.